Fresh bedding - Copymaster3D 300
Intro
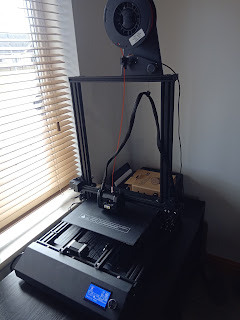
Unfortunately my heated bed is not flat. In fact it is 0.5mm lower in the middle than it is the corners!
With a bit of compensation, I could print to a good standard but as things ventured towards the edges, it all got a bit too close to the bed and things started to get messy.
Talking to the shop
Of course going back to the manufacturer to sort out a problem with a new printer was not the first thing that comes to my mind. That would be sensible. but I did try to talk to Technology outlet. These are the main UK distributer for Copymaster3D and the place I bought mine from.
To their credit they were very quick to respond to my problem. Their responce was:
Now I am all for bodging things but is this really the correct answer to rectify a manufacturer problem with a new product? It shouldn't be down to me to fix a quality control problem and especially bodging a heated bed with masking tape! What insensed me more was the comment on the screws causing this. This was later clarified as the springs causing an upward bending force on the bed when I questioned this. This still didn't work and now I fealt fobbed off. I replied with a long winded explenation on how bending moments worked in this situation but ultimately just felt like I was wasting mine and their time. I had already resigned myself to the fact that this is a cheap product and as such I should "have to accept" the low quality that will come with that.
"...0.5mm is within manufacturing tolerances. It will always deviate slightly due to the 4 screws in the corner applying a constant pulling force.
What you can do if you cannot get a print down, is to raise the middle, you can apply 3-4 strips of wide masking tape across the centre, it will raise it slightly..."
Finding a new bed
A bit of online searching told me that I should buy some borosilicate glass to cope with all the heat. A little more time however showed that plenty of people had been using glass tiles and even mirrored glass.
I was all set to pop to my local hardware shop to see if they had glass tiles when I remembered I had a broken window unit sat in the garden waiting to go to the tip. This would do the trick and if it didn't it wouldn't really matter if it broke as it was going in the bin anyway.
Cutting to size
I knew the sheet of glass was too long so bought a Silverline lubricated glass cutter from ebay along with some bulldog clips and waited on its arrival.
When the tool had arrived I dug out the window unit. It must have been bigger in my mind as it was too narrow. Regardless I separated out the laminations, binned the broken side cleaned up the side I would use.
On the right is a video that I found helpful although I did not mark twice like this guy does. I don't see the point.
I measured the 320mm I needed and marked this with a marker pen in a couple of places then joined the dots with a rule and scored a cut line.
I was using a plastic rule which was less than ideal as the cutter really needs a steady hand or it will wanted off. This gave me a few false start cut lines on the surface. I then placed a thin nail under the score line and gently pressed down on either side of the score line.
The glass cracks suddenly but undramatically following the score line from the point of stress (that nail). Unfortunately it did veer off along a false start score line. Knowing this was probably not going to get used as was too narrow, I experimented at tidying this up. Another score line was made and the excess cut off. This worked less well as I had less leverage whilst braking but it did take the bulk of it off. I finished up the odd bits on the bench grinder. Holding the item firmly with gloved hands and a light pressure successfully removed the rough bits without shattering the glass or firing it across the garage.
I had learned a fair bit doing this and remembered I had a spare green house glass pane sat in the green house so grabbed than and had another go at it. I used a steel rule this time and put a bit more pressure into the cut which came out successfully for both cuts require for my 320x320 bed.
The new sheet of glass was then given a good clean before I dragged it inside.
I removed the magnetic bed and fit the glass bed with the 15mm bulldog clips I had bought. These are absolutely maxed out here so I would suggest going slightly bigger if you can.
When the tool had arrived I dug out the window unit. It must have been bigger in my mind as it was too narrow. Regardless I separated out the laminations, binned the broken side cleaned up the side I would use.
On the right is a video that I found helpful although I did not mark twice like this guy does. I don't see the point.
I measured the 320mm I needed and marked this with a marker pen in a couple of places then joined the dots with a rule and scored a cut line.
I was using a plastic rule which was less than ideal as the cutter really needs a steady hand or it will wanted off. This gave me a few false start cut lines on the surface. I then placed a thin nail under the score line and gently pressed down on either side of the score line.
The glass cracks suddenly but undramatically following the score line from the point of stress (that nail). Unfortunately it did veer off along a false start score line. Knowing this was probably not going to get used as was too narrow, I experimented at tidying this up. Another score line was made and the excess cut off. This worked less well as I had less leverage whilst braking but it did take the bulk of it off. I finished up the odd bits on the bench grinder. Holding the item firmly with gloved hands and a light pressure successfully removed the rough bits without shattering the glass or firing it across the garage.

The new sheet of glass was then given a good clean before I dragged it inside.
I removed the magnetic bed and fit the glass bed with the 15mm bulldog clips I had bought. These are absolutely maxed out here so I would suggest going slightly bigger if you can.
As I had compensated for a wobbly bed before I had to re set my Z offset which I performed as before.
It is worth noting in the image above that I had 6 clips fitted. I later removed the middle two and flipped the bed when I realised I was forcing the glass to conform to the bent bed shape of the heated deck.
Once all was set up and glue stick applied I performed a few test prints which were bonding to the new surface well with no damage to the glass yet.
It is worth noting in the image above that I had 6 clips fitted. I later removed the middle two and flipped the bed when I realised I was forcing the glass to conform to the bent bed shape of the heated deck.
Once all was set up and glue stick applied I performed a few test prints which were bonding to the new surface well with no damage to the glass yet.
Comments
Post a Comment